Keeping your trucks running smoothly is straightforward. The key lies in regular maintenance checks, spotting problems before they worsen, tracking fleet status, and implementing prevention-focused strategies. Regular inspections and repairs guarantee reduced interruptions, better productivity, and protection. Expert guidance from experienced technicians will guide you through fleet maintenance through the effective use of tech solutions, detailed logging, and skilled personnel. Go ahead, immerse yourself in this complete guide to fleet maintenance and discover cost-effective operations. There's so much to discover and understand!
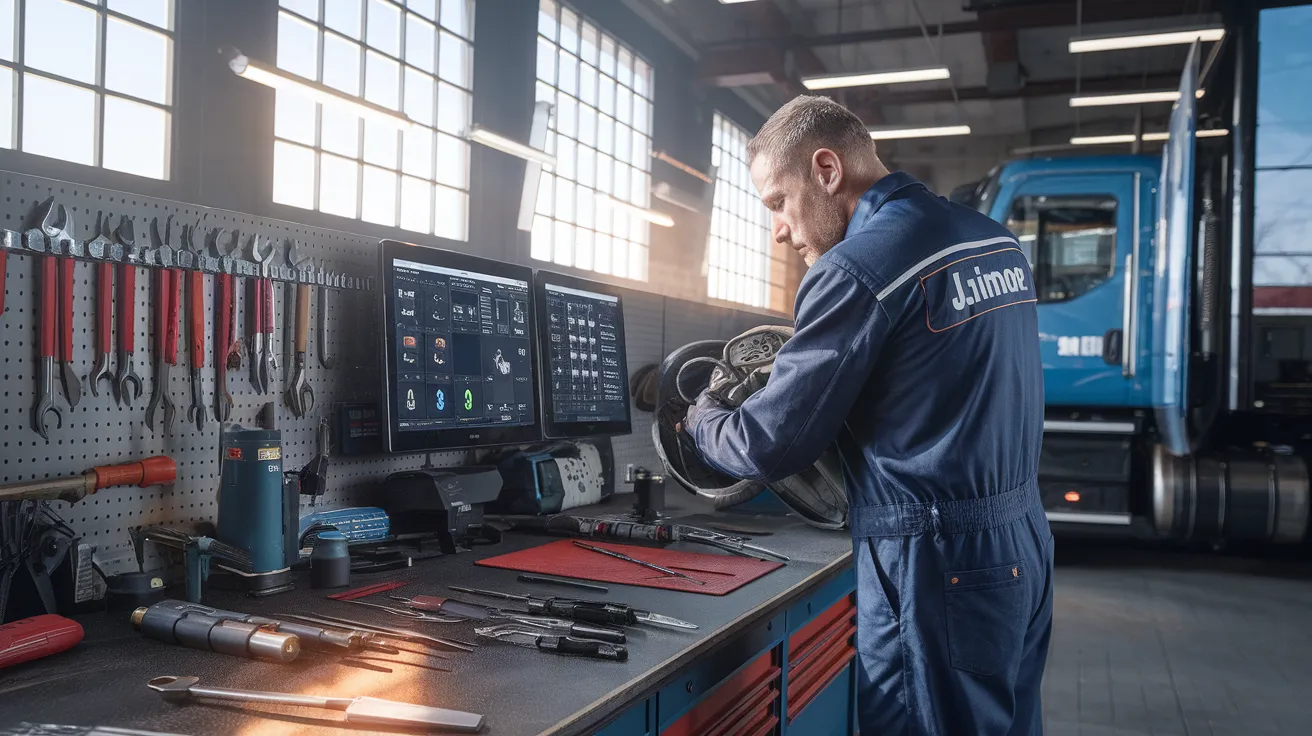
Main Insights
Understanding the Critical Role of Regular Truck and Fleet Upkeep
Although it might seem daunting, getting a handle on proper fleet and truck maintenance is vital for every prosperous company. The benefits of maintenance greatly surpass the resources you put in. Consistent checks and upkeep can significantly extend the lifespan of your vehicles, preventing expensive replacements. Moreover, there's a clear link between well-maintained trucks and improved fuel efficiency. This translates to lower fuel costs, boosting your total operational efficiency. Moreover, regular upkeep can detect minor issues before they develop into major issues, saving you expensive repair costs in the future. Therefore, don't underestimate the value of regular upkeep; it can be a true difference-maker for your company's profitability.
Identifying Critical Aspects of a Well-Planned Maintenance Program
To guarantee your fleet's longevity and efficiency, it's crucial to identify the fundamental aspects of a successful maintenance program. You'll need to understand the basic principles of maintenance, assess the condition of your fleet consistently, and establish preventive measures in advance. With these in place, you're well on your way to decreasing downtime and enhancing productivity.
Fundamental Maintenance System Elements
If you're looking to boost your fleet's efficiency and lifespan, creating a robust maintenance program is crucial. Critical elements of the program include regular inspections, regular servicing, and proactive repairs. Every component is instrumental in preventing expensive failures and limiting downtime. While the advantages of a maintenance program are numerous, don't ignore the implementation challenges. These can range from logistical issues and team reluctance. However, with strategic organization, effective messaging, and dedication to training, these obstacles can be overcome. Remember that an well-designed maintenance program goes beyond fixing problems; it stops them from occurring. It's an investment in your fleet's longevity – and it's one that pays dividends.
Fleet Condition Monitoring
As you delve into the key elements of a successful maintenance program, recognizing the significance of fleet condition monitoring takes center stage. It's not just about keeping your vehicles running, it focuses on optimizing fleet performance. Monitoring technologies offer a thorough view of your fleet's health, allowing you to detect potential issues before they escalate.
Such tracking solutions measure vital parameters like fuel consumption, tire pressure, engine health, and more. By leveraging this data, you're not only ensuring the durability of your fleet but also minimizing avoidable maintenance expenses. Keep in mind timely discovery is key in fleet management. So, adopt reliable monitoring systems and stay ahead of the curve. Don't merely address problems, predict them. Monitor your fleet's status regularly and your enterprise will perform optimally.
Setting Up Preventive Strategies
While keeping tabs on your fleet's condition is essential, establishing preventive protocols is equally critical to ensure a successful maintenance program. It's important to identify potential concerns before they develop into major repairs and equipment downtime. So, let's talk preventive measures.
One effective approach is creating a detailed maintenance checklist. This checklist should outline all necessary inspections, tune-ups, and component updates. Routine engine monitoring, tire rotations, and oil changes are essential. Make sure to include basic components like wiper blades, illumination, and filters.
Make sure your checklist contains a timeline for every maintenance item. Adhering to this schedule guarantees that your fleet remains in peak condition. Keep in mind, preventative care reduces expenses, time, and problems down the road.
Essential Routine Checks for Transport Fleet Care
To make certain your truck and fleet stay in peak condition, you should emphasize regular maintenance checks. These assessments encompass scheduled maintenance inspections and essential system reviews. By maintaining these vital protocols, you'll maximize your fleet's lifespan, optimize operational performance, and in the end, save on major repair expenses.
Routine Equipment Inspections
Regular maintenance inspections serve as your primary safeguard against sudden fleet and vehicle failures. They provide you a chance to detect and fix concerns before they turn into costly repairs or dangerous accidents. One of the most significant benefits of routine maintenance is the avoidance of service interruptions, which can greatly impact your company's productivity and bottom line.
Key Component Evaluations
Building on the critical nature of scheduled maintenance inspections, let's move towards the specific essential component checks that ought to be conducted regularly to guarantee optimal truck and fleet performance. First examine the brake system – verify all components are operating correctly, from brake pads to fluid levels, and checking for leaks. Neglected, brakes could fail, leading to serious incidents. Checking tire pressure is equally essential. Low pressure raises fuel consumption and tire wear, while excessive pressure risks a blowout. Purchase a high-quality pressure gauge for precise readings. Keep in mind tires should be cold during checks for optimal results. Consistently conducting these essential checks can help avoid costly repairs and potential accidents. Stay safe on the road.
Strategic Maintenance Planning for Fleet Optimization
In fleet management, it's vital that you prioritize preventative maintenance to guarantee peak efficiency. Setting up a systematic preventative scheduling system is key. This reduces unnecessary wear and tear, and reduces the likelihood of unscheduled downtime. You must arrange regular checks and servicing based on engine hours, mileage, time, or fuel usage. Keep in mind each vehicle is distinct and might need a customized approach.
Maintenance education serves as a crucial approach to maintain peak efficiency. Equip your team with the necessary skills to detect potential issues early on. This not only saves time but also lowers operational costs. The integration of preventative scheduling and maintenance training will create a more productive and reliable fleet. Proactive maintenance always trumps reactive repairs.
Expert Recommendations for Transport Fleet Maintenance and Recovery
While fleet and truck maintenance and restoration might appear challenging, knowing the basics can help simplify things. The first thing you should do should be to understand various repair techniques. This understanding will enable you to diagnose concerns swiftly and accurately. Following this, arrange repair tasks depending on how serious the issues are and the truck's function in your operation. Regularly inspect each vehicle for potential issues and tackle them quickly to avoid additional problems. Remember, restoration isn't just about fixing issues, it's aimed at upgrading the unit's efficiency and durability. Finally, consistently choose high-quality parts for repairs; they'll last longer and perform better. Remember these guidelines, and you'll handle fleet maintenance and renovation with ease.
Leveraging Industry Innovations for Enhanced Fleet Management
To stay ahead in the trucking industry, it's essential to harness innovative solutions for advanced fleet maintenance. New technologies are revolutionizing the maintenance landscape. Implement data analytics to monitor your fleet's performance and identify problems before they arise.
State-of-the-art monitoring systems keep track of engine health and efficiency, fuel consumption, and driving habits. Utilize these insights to implement preventive maintenance, helping reduce costly operational interruptions.
Always prioritize software updates. These improvements generally deliver crucial updates and fixes that boost your automotive fleet's safety and performance. Remember maintaining your fleet involves more than basic repairs. You're conducting business in a digital period, and following technological advances will promote your fleet's durability and profitability. With appropriate processes, you can lower expenses and effort, and enhance safety measures.
Questions & Answers
What Requirements Must a Skilled Fleet Maintenance Mechanic?
You will require a valid certification, fulfilling the standards of a recognized mechanic institution. Furthermore, you must pass a comprehensive skill assessment, proving your knowledge in multiple facets of fleet service and repair. Professional experience is also important!
When Should I Change the Tires on My Fleet Vehicles?
Similar to clockwork with the changing seasons, you need to examine your fleet's tire wear periodically. Nevertheless, it's generally recommended to swap out tires every three to six years, based on road conditions and usage patterns.
What Are the Common Signs of Engine Trouble in Trucks?
You'll spot engine trouble in trucks by signs such as abnormal engine noises or even poor fuel performance. Additional indicators are heavy smoke emissions, oil leaks, or a check engine light that won't turn off.
How Does Technology Impact Truck and Fleet Maintenance?
Technology is crucial in optimizing truck maintenance. Telemetry systems deliver real-time data, while predictive analytics help prevent issues before they happen. You'll notice reduced downtime, improved safety and in more info the end, cost savings. It's revolutionary.
How Do Maintenance Needs Vary Across Fleet Vehicle Types?
Different vehicle types certainly require specific maintenance schedules. You need to consider the vehicle's function, weight limits, and terrain type, as these aspects substantially impact required servicing. Always adjust maintenance based on the vehicle classification.
Conclusion
In the end, what matters most is maintaining optimal fleet performance, right? Routine maintenance isn't merely a recommendation, it's a must. By pinpointing crucial elements, performing regular inspections, using preventative strategies, and harnessing industry innovations, you're not just maintaining your trucks, you're honing a well-oiled machine. And remember, vehicle maintenance isn't a setback, it's a chance for improvement. Stay committed, and you'll experience your fleet's efficiency, reliability, and longevity reach new heights.